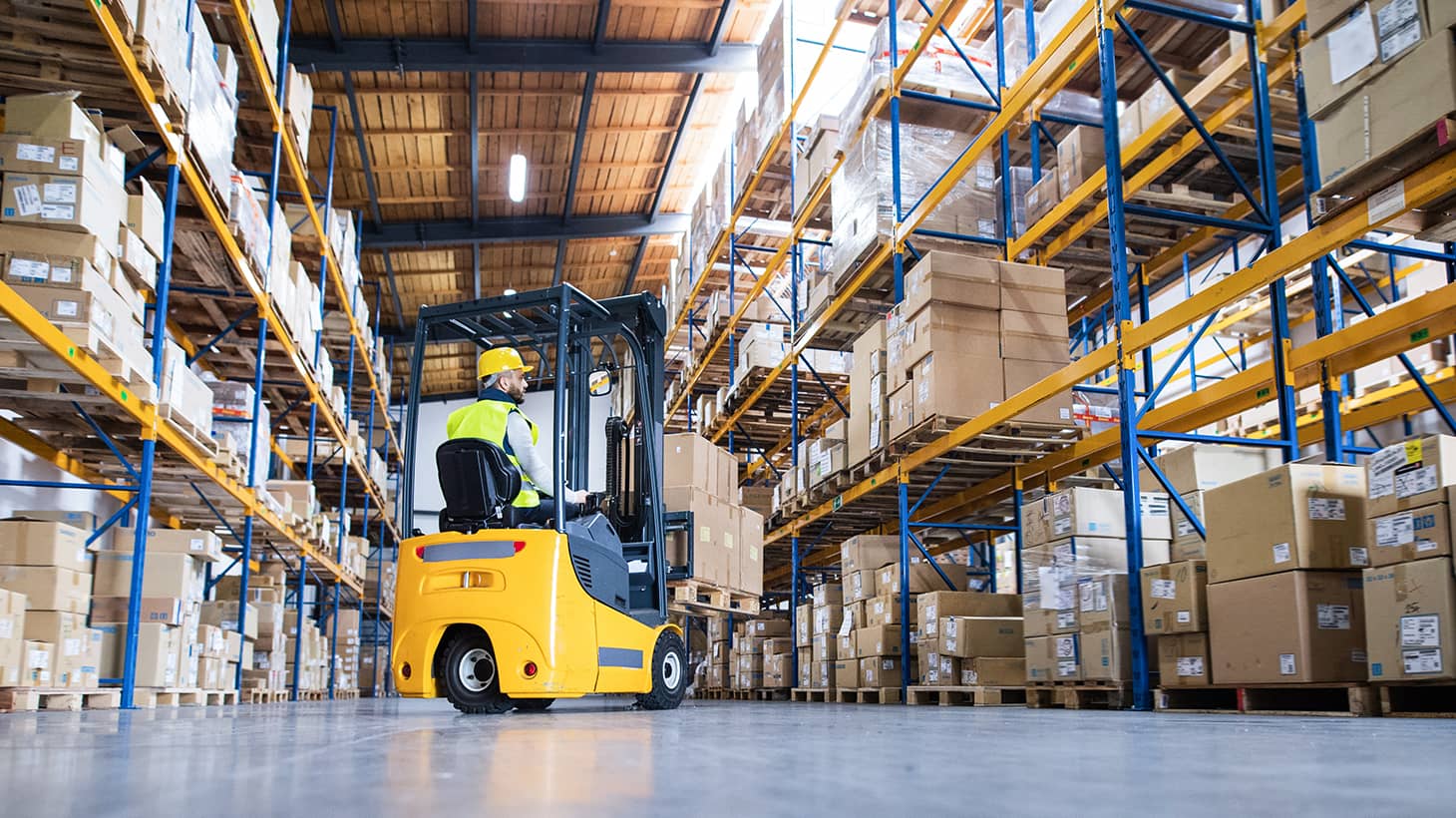
What is Slotting Optimization?
In this article we will provide a comprehensive guide on what warehouse slotting is, how to implement proper warehouse slotting optimization, the benefits of warehouse slotting optimization, the components and features of the best slotting optimization software, and everything else you need to know to maximize operational slotting efficiency profitably for your warehouse or distribution center.
What is Slotting Optimization?
What Slotting Optimization is and How to Execute it Profitably
Having everything in its right place is key to executing proficient workflow processes for any operation, but it’s especially important when storing and distributing desired goods. You don’t want short life-cycle products or products in high demand in a difficult place to access, heavily packaged items in locations where they could be damaged or can damage other products, or warehouse space left unutilized. Inefficient slotting can lead to abandoned products, resulting in wasted time finding desired items, which leads to an exhausted workforce, unmet SLAs, and an increase in the probability of damaged goods.
However, the best warehouse slotting optimization software can lead to profitable business outcomes, including advanced order accuracy, productive fulfillment processes for maximized throughput, seamless fulfillment for all selling channels (digital and physical), and automotive technology capabilities that place inventory in the optimal location—considering factors such as seasonality, sales trends, product variations, and more—leading to improved customer satisfaction and measurable results.
Slotting optimization differs from allocation optimization. Allocation optimization strategies and processes often relate to placing items in the optimal location of a retail store or marketplace to execute more efficiently on customer-facing inventory. Slotting optimization focuses on the backend—warehouse or distribution center (DC)—inventory and placing products in the optimal slot for picking and distributing.
Essentially one makes life easier for customers to get the product they desire while placing customer-facing inventory in the prime position to maximize profits, and the other makes it easier for warehouse workers to retrieve the right product in a timely, efficient, and cost-effective manner. There may be some instances where these systems benefit from unification—for example in a warehouse store setting where pallets are also involved in customer-facing inventory.
What is Slotting Optimization?
Slotting optimization is the process of organizing, managing, planning, and placing inventory in the optimal storage slot location of a warehouse or DC for maximum fulfillment efficiency. This location is determined by numerous factors, including product characteristics, composition, demand, lifecycle, type, warehouse or DC layout, and SKU. The best slotting optimization places inventory in the ideal location to improve operational efficiency and agility, gets high-demand products out of the door faster without compromising or negatively affecting other inventory, optimizes pick paths, reduces dock and aisle congestion, and provides differentiating business results that enable users to stay ahead of the competition.
For many slotting optimization software users, the process of picking a slot via a forklift, placing the slot on a pallet, and loading that pallet onto a truck or carrier service is accomplished quickly, easily, and in the most cost-effective manner for the business and workforce.
The ideal slotting optimization utilizes automation software capabilities that automatically determine the best locations to pick inventory. This is accomplished through the software's ability to strategically group items for fulfillment and update placement recommendations based on trends and new product demand—effectively increasing workforce efficiency, shortening order fulfillment cycles, and maximizing throughput.
Manual slotting optimization, on the other hand, can be a cumbersome task for warehouse workers who do not utilize adaptive or unified solutions that share data across warehouse management systems (WMS), transportation management systems (TMS), labor management systems (LMS), and slotting optimization functions. Requiring access to data from multiple siloed systems or manual data entry can result in miscalculations or operational assumptions, which can negatively affect space utilization planning. The best slotting optimization systems allow users to automate wherever needed based on business and warehouse needs, performing complicated tasks so workers can focus on less time-consuming and tedious responsibilities.
Challenges of Slotting Optimization
The challenges of slotting optimization depend on the business needs, the type of technology used, and the available resources of the supply chain. Challenges may include capacity constraints, labor productivity, disconnected systems, an inability to understand or identify where the improvement opportunities are in slotting, legacy technology, lack of system- and network-wide standardization, lack of system flexibility, integration issues, inaccurate data, unpredictable demand, and changing picking patterns.
Labor productivity: Lack of the required labor or labor management systems that are either legacy or not unified with other systems can reduce the productivity potential of the workforce when utilizing slotting optimization.
Disconnected systems: Without unified data and visibility of all supply chain solutions, siloed systems can act counterproductive to one another, which leads to inefficient slotting optimization.
Inability to understand or identify improvement opportunities: A lack of enterprise-wide visibility or an inability to see or identify data points that detail where slotting can be improved can make knowing where to apply slotting optimization difficult. This can be due to legacy technology that does not properly use advanced algorithms or analyze data to suggest where slotting can be improved.
Lack of system- and network-wide standardization: Enterprise businesses with multiple DCs need connected solutions that can locate and solve problems throughout the entire distribution network to apply and standardize the optimal workflow.
Lack of system flexibility: Systems must be able to adapt to various business slotting needs and changes in product demand, sales trends, and product variations with flexible solution capabilities, including the ability to reset pick locations, configure run strategies based on real-time picking patterns in the warehouse, and group items together for faster fulfillment.
Insufficient Integration: Whether it’s an inability to integrate seamlessly with existing daily workflow tasks or a lack of integration with other software applications, lacking sufficient integration will lead to inefficient processes.
Unpredictable demand: Being able to predict demand accurately is a vital piece to the puzzle with slotting optimization and if your systems cannot analyze historical and forecasted data to develop strategies and workflows based on future product demand it can lead to a plethora of challenges to overcome in the DC. These challenges include improper space utilization, time-consuming or changing pick paths, unmet service level agreements (which reduces customer satisfaction), and higher labor costs.
Benefits of Slotting Optimization
As mentioned above, the best modern slotting optimization solutions maximize DC or warehouse throughput by placing items in the slot or shelf for maximum fulfillment efficiency based on numerous calculated factors. This is done without compromising other product priorities and without the need for extra labor or storage space. When utilized correctly, slotting optimization leads to significant benefits for everyone involved—the business, supply chain planners, third-party vendors, and warehouse workers. The benefits of effective warehouse slotting include:
Increased picking efficiency: Items are placed in the ideal location for workers to retrieve and are done so following demand and product characteristics. This reduces unnecessary or time-consuming pick paths, improves picking accuracy, and provides faster order picking, packaging or receiving, and shipping.
Reduced labor costs and travel time: Travel time for picking tasks is reduced by placing inventory in the optimal location for fulfillment. Items are placed logically with fast-moving inventory in the right, easy-to-access location and not on opposite sides of the warehouse. Seasonally-based items are available when needed (and out of the way when not), and sales trends are accounted for. As a result, items are positioned in the ideal location, enabling fewer labor strains or labor required to gather items for every slot, leading to reduced labor costs.
Improved inventory accuracy and control: Slotting optimization enables users to ensure that inventory is always in the correct place and can be moved easily to adapt to any business or supply chain need. Even the most complex slotting environments can be controlled with the right slotting optimization software that can set and re-set pick locations based on product demand, group items for quicker fulfillment, update product placement, and run multiple strategy configurations based on real-time picking patterns.
Optimized space utilization: The best slotting optimization tools consider the total layout of a given warehouse or distribution center and maximize the space provided to get the most out of each slot provided. If shelves are being utilized, slotting optimization stacks products efficiently by calculating factors such as weight and size, and places high-demand products in easy-to-reach locations, effectively maximizing the square footage available.
The Optimal Approach to Slotting Optimization
Manhattan Active® Slotting Optimization utilizes intuitive and easy-to-leverage built-in learning intelligence that continuously calculates optimal slotting. It automatically determines the best locations to place inventory to increase workforce efficiency, shorten order fulfillment cycles, and maximize throughput. It also improves customer service by strategically grouping items for fulfillment and updating placement recommendations based on trends and new product demand.
The solution adapts to business needs by considering seasonality, sales trends, and product variations, while maintaining preferred-item sequencing and family groupings. It is designed with capabilities to handle even the most complex warehouse environments.
Manhattan Active Slotting Optimization delivers the first and only seamless unification of slotting moves and picking, engineered as part of overall DC management. As a single application—natively unified with warehouse management, labor management, and yard management—it requires no integration or modifications to ensure decisions are executed in the most timely and cost-effective manner.
It requires no intervention from the user with pre-seeded, slotting-run strategies that streamline configuration and provide unprecedented flexibility, whether manually executed on demand or easily scheduled ahead of time. Further, it is part of the same application as Manhattan Active® Warehouse Management, providing a consistent intuitive, mobile-user experience integrated across the enterprise.
By driving optimal efficiency in slotting workflows, Manhattan’s slotting optimization data analysis and location recommendations, visualization tools, seamless integration, and flexibility produce results such as reduced replenishment and increased throughput volume. Beneficial solution outcomes include:
- Intelligent, adaptable, and faster picks: Sets and re-sets pick locations based on product demand, changing consumer expectations, and operational constraints. It also enables faster picking due to product SKUs living in the correct and optimal aisle, pallet, and slot.
- Smarter fulfillment: Groups items for rapid fulfillment and updates item placement based on sales trends and product variations.
- Calculated placement: Uses product characteristics and velocity to calculate a relative value for each potential placement.
- Advanced algorithms: Aggregates values across products and compares millions of move combinations against user-configured strategies. Configures multiple run strategies to ensure optimal configurations based on real-time picking patterns in the warehouse.
Why Manhattan Active® Slotting Optimization?
Slotting optimization is as important now as ever with the rising need for ecommerce fulfillment, which is only expected to continue to increase. In a recent report from Prologis Research, “Online share of goods spending will continue to increase (from 15% in 2019 to 25% by 2025), which will continue to drive the need for more space as ecommerce requires three times the logistics space compared to brick-and-mortar retail.”
Combine these trends with other operational challenges that include smaller orders, SKU proliferation, volatile demand, and shorter order cycle times, and the right slotting optimization can have a large impact on controlling costs and meeting modern customer expectations.
Contact our team to request a demo and see for yourself the business and operational benefits of Manhattan Active Slotting Optimization.
Deliver On Your Promise to Customers
Get in touch with the Manhattan team to see how we can help.
Supply Chain Commerce Solutions
Manhattan offers a complete breadth of solutions that when unified, provides total coverage for your supply chain commerce needs.