Unlocking Potential: The Future of Unified Supply Chain Technology
- 5 August 2024
- Blake Coram, Director, Product Management
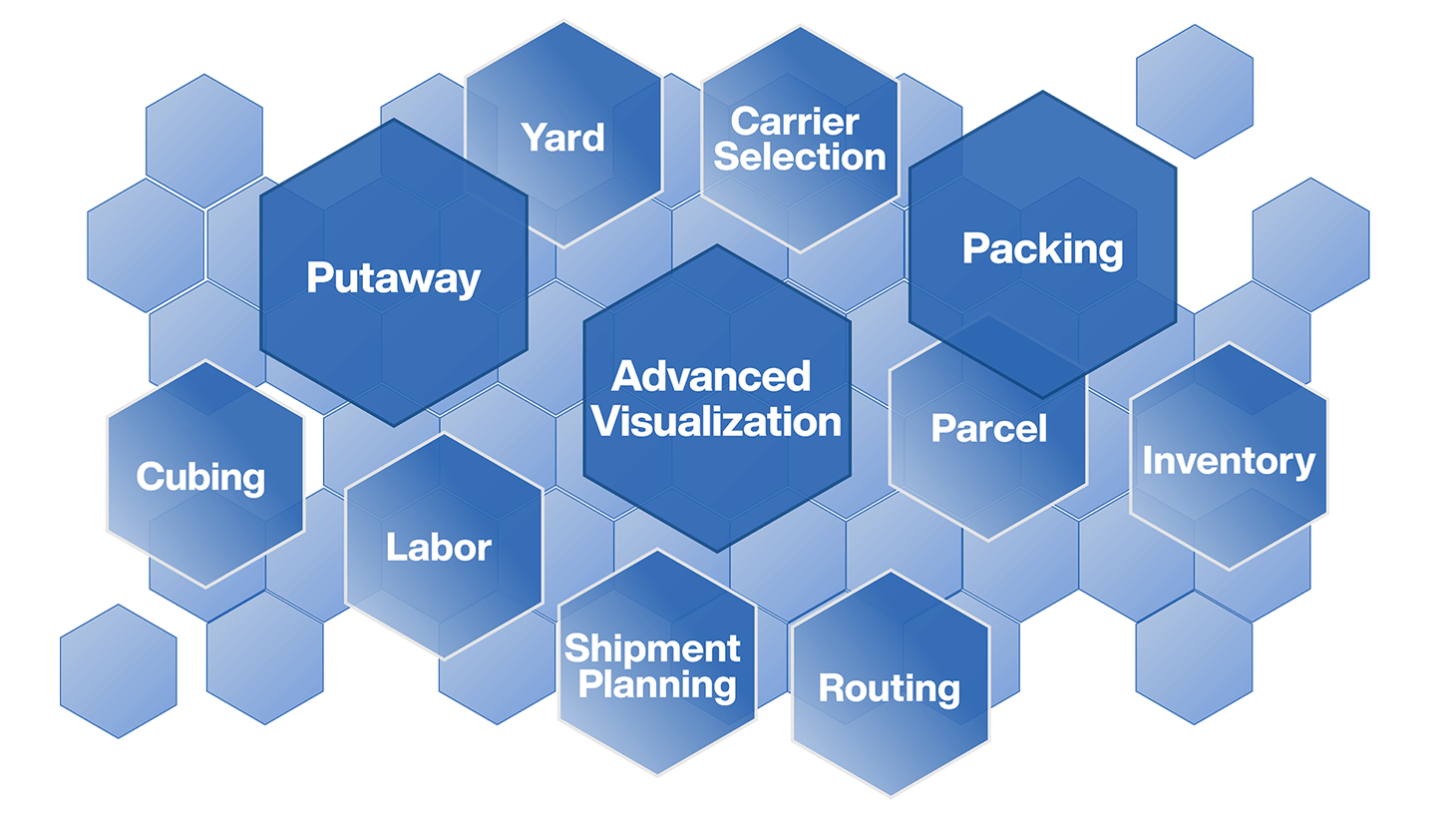
Today’s dynamic logistics landscape demands a shift from siloed and integrated approaches to unified supply chain operations. The future hinges on building fully unified systems that transcend application boundaries and share information throughout the logistics ecosystem. Let’s delve into the potential unleashed when artificial barriers between supply chain solutions are removed, and these applications operate in unison. We’ll define a unified supply chain, discuss the relevant systems involved, and explore the enabling changes. Finally, we’ll examine the use cases unlocked in this unified environment. First, let’s clarify the concepts.
Unified Supply Chain Systems
Supply chain unification is a transformative approach to logistics management. By dismantling barriers between systems, organisations achieve seamless execution and optimisation, unlocking unprecedented performance levels. Gartner analysts define supply chain convergence as traditional systems operating across application boundaries to execute and optimise functions. Unified supply chain systems push this concept further by eliminating these boundaries.
Traditional Supply Chain Systems
When we talk about supply chain systems, we’re referring to established frameworks that facilitate the execution of supply chain operations. These systems could be siloed or integrated and have lagging and limited data sharing. Typically, these systems fall into three main categories:
- Transportation Management System (TMS): This system involves activities such as negotiating with carriers, managing internal fleets, and optimising shipping routes to meet logistical needs efficiently.
- Warehouse Management System (WMS): Here, the focus is on receiving, storing, picking, and shipping products while ensuring alignment with transportation commitments and optimising labour usage.
- Yard Management System (YMS): Acting as the bridge between transportation and warehouse functions, yard management systems oversee the flow of goods between trucks and facilities.
Unified Supply Chain Systems Operate Differently
The journey towards supply chain convergence began over a decade ago. Recent advancements in cloud technology have since played a crucial role in enabling this transition. Cloud-native architecture allows for a move towards composable components, fostering seamless information sharing between different elements. Moreover, this advanced architecture ensures that systems remain evergreen, able to evolve rapidly and offer access to continuous innovation.
Here are three use cases that demonstrate how unified supply chains operate differently.
Use Case: Pre-Plan Flow
In a traditional approach, orders flow into the TMS for planning, with an interface into the WMS for execution (Figure 1). However, once that shipment plan is transmitted, the TMS is locked in without the ability to adjust or reoptimise, even with new orders entering the system. The TMS lacks detailed insight into WMS execution, receiving only aggregate feedback. Details such as allocations, cubing, pallet creation, and pick/pack issues remain unknown to the TMS until shipping.
Figure 1: Traditional Integrated Systems: TMS + WMS Pre-Plan Flow
In a unified solution, the TMS gains comprehensive access to execution details (Figure 2). This enables shipment planning to continuously re-evaluate and optimise, responding to facility fluctuations and last-minute order changes in real time. New orders seamlessly integrate into the plan as shipment planning remains aware of ongoing execution progress. This heightened awareness significantly influences planning decisions, with warehouse components like allocation and cubing directly impacting shipment planning outcomes.
Figure 2: Unified System: TMS + WMS
In legacy integrated or standalone solutions, planning typically operates well below actual capacity of the trailer due to expected exceptions that occur during warehouse operations. However, in a unified environment, organisations can leverage real-time data from warehouse management to optimise shipment planning, allocating resources efficiently to their full capacity.
Most inventory exceptions stem from allocation/cubing variations. By aligning planning with real-time fluctuations during waving, packing, and shipping processes, and by eliminating “safety space” in trucks, organisations can significantly increase trailer utilisation by informing planning about exceptions up front. This real-time knowledge of warehouse inventory and operations enhances the accuracy of expected shipping quantities, leading to improved trailer utilisation by eliminating unnecessary buffers to capacity.
The benefits extend beyond shipment planning, with improvements seen throughout the supply chain. Let’s explore these benefits beyond the warehouse, moving to the yard.
Use Case: Dynamic Live Trailer Interleaving
At distribution centres, teams understand the importance of coordinating live trailer operations to prevent disruptions and avoid detention charges. Typically, dock space is allocated based on average expectations, leading to underutilisation or overutilisation due to daily fluctuations (Figure 3).
Figure 3: Dedicated Docks
Unified supply chain technology streamlines this process (Figure 4). After unloading, the YMS automatically manages empty trailers and plans the next steps based on factors like warehouse unload times and transportation-driven factors such as live trailer ETAs. By seamlessly integrating live unloads into the warehouse receiving process, the need for dedicated live dock space and related inefficiencies is eliminated.
Figure 4: Dynamic Planning
Use Case: Optimised Putaway Travel
In a unified supply chain, the yard management system can enhance decision-making by delving into facility details. For instance, in putaway execution, the chosen receiving door significantly affects travel distance (Figure 5).
Figure 5: Traditional Putaway Path
In legacy solutions, tribal knowledge often guides door assignment decisions. More advanced integrated solutions might even leverage rules-based assignment. However, neither of these provide truly optimised execution. With unified systems, all necessary information is seamlessly shared between components for optimal decision-making such as warehouse layout and putaway strategy, thereby promoting efficiency and accuracy (Figure 6).
Figure 6: Putaway with Unified Systems
The Journey to Unified Supply Chain
Embracing a unified supply chain approach creates opportunities for new levels of efficiency, sustainable growth, and competitive advantage. By breaking down traditional barriers and embracing innovation, organisations can enhance efficiency, visibility, and collaboration across the logistics ecosystem. While the journey to supply chain convergence continues, the potential rewards are substantial. Unified technology empowers businesses to navigate modern logistics with confidence, agility, and resilience.
Related Insights
Manhattan offers a complete breadth of solutions that when unified, provides total coverage for your supply chain commerce needs.
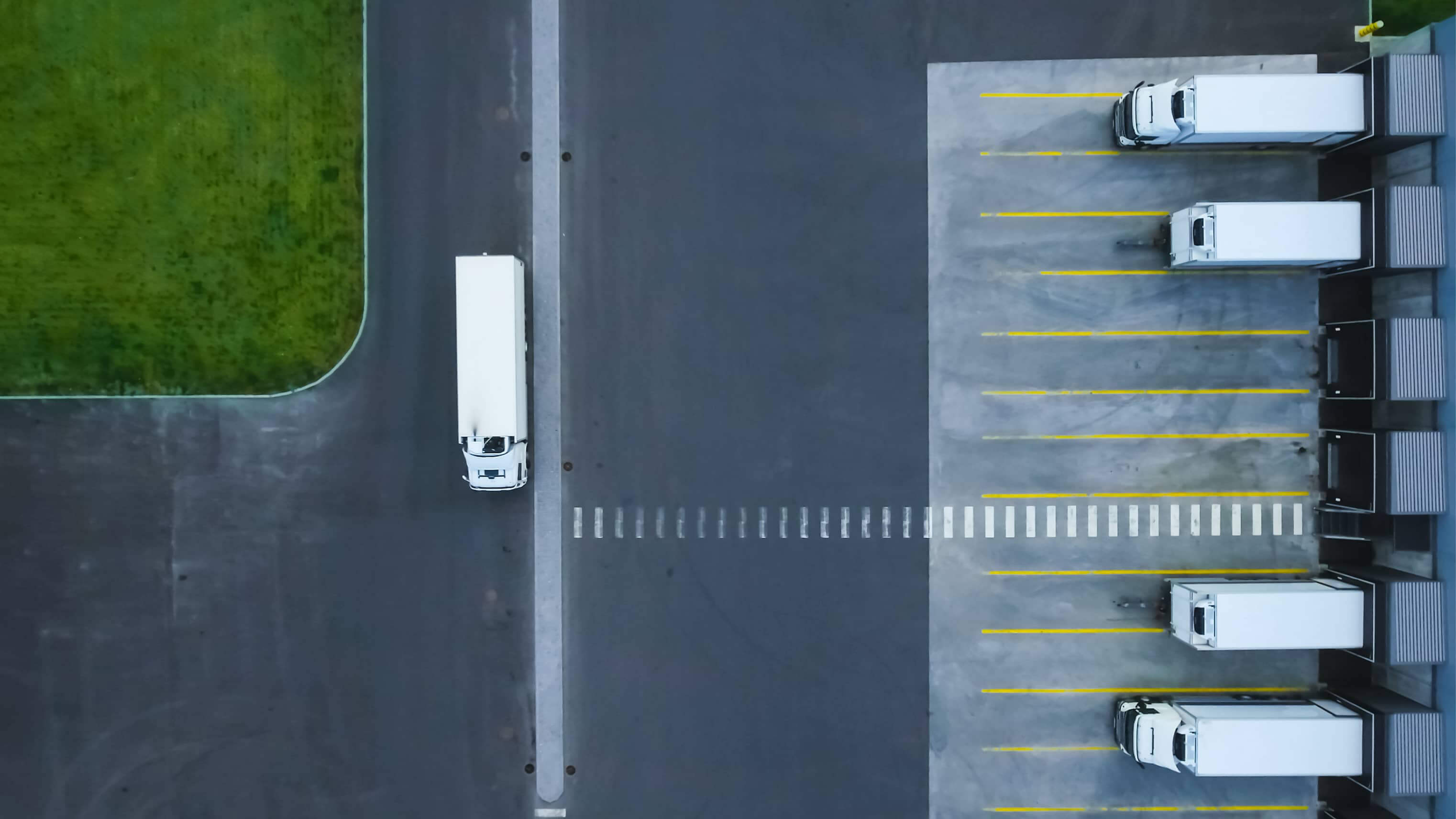
Yard Management
Unify yard operations, boost efficiency, and enhance visibility with Manhattan Active® Yard Management—a solution that allows you to adjust to unexpected situations and uncover opportunities for performance optimisation and cost savings. With Yard management, Manhattan has completed the digital unification of distribution and logistics where they come together in the physical world.
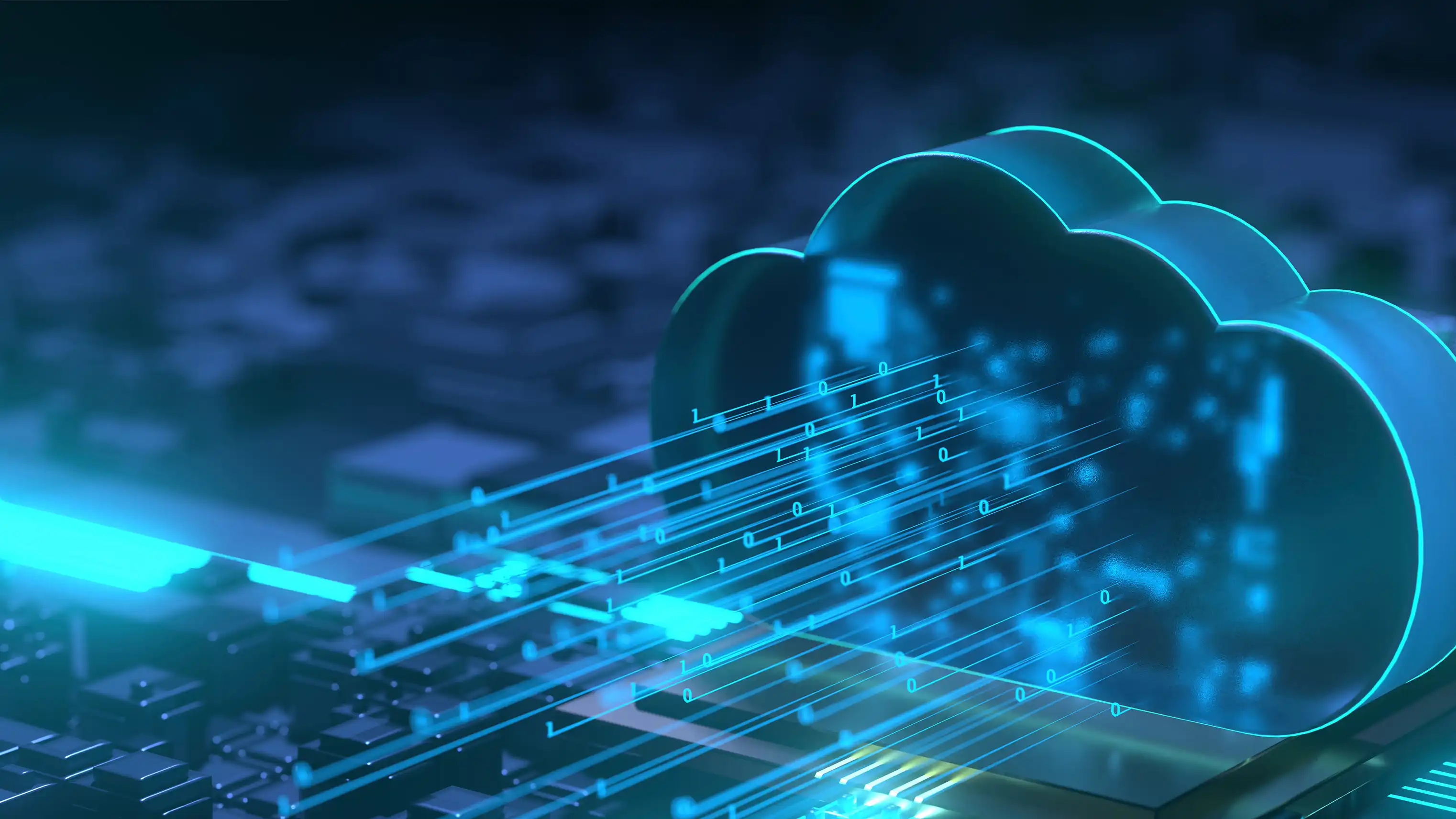
Manhattan Active® Platform
Learn about Manhattan Active Platform, the core of Manhattan Active solutions flexibility and resiliency.
Transportation management
Our transportation management system makes your job easier. How? With applied intelligence and network connection speeds up to 10x faster than other systems.