Fresh Success: Revolutionizing Grocery Retail with Manhattan
- January 24, 2024
- Manhattan
Demand Forecasting and Replenishment in Retail Grocery
In the competitive world of grocery retail, managing fresh food inventory remains one of the most challenging aspects. Fresh foods—fruits, vegetables, dairy, and bakery items—demand a fine-tuned balance between supply and demand due to their short shelf lives and fluctuating consumer buying patterns. This is where Manhattan’s Demand Forecasting and Replenishment software comes into play, offering an innovative solution tailored to the unique challenges of fresh food management.
Understanding the Challenges of Fresh Foods in Grocery Retail
Fresh food items are particularly susceptible to wastage, with factors like seasonal availability, quality deterioration, and unpredictable consumer preferences impacting inventory management. Grocers must ensure that fresh items are not only in stock but also of the highest quality to meet consumer expectations. Overstock leads to spoilage and waste, while understock can result in lost sales and customer dissatisfaction.
A Grocery Retail Fresh Advantage With Manhattan
Manhattan’s software addresses these grocery retail challenges through advanced technologies, including AI, machine learning, and sophisticated analytics. Here's how it benefits grocers handling fresh foods:
-
Precision in Demand Forecasting
The software's AI-driven algorithms analyze various data points—from past purchasing trends to weather forecasts and local events—to accurately predict demand. This precision is crucial for minimizing waste and ensuring the availability of fresh foods, where sales can fluctuate dramatically.
The application goes beyond mere forecast calculations; it meticulously examines product day-to-day demand history patterns and seasonality patterns, addressing data anomalies and mitigating spikes. By auto-generating day-of-week profiles that accurately represent the genuine daily demand patterns of each SKU, the system ensures a high level of precision. This automated process adapts seamlessly to evolving demand patterns without the need for manual intervention, significantly enhancing forecast accuracy.
Moreover, the application effortlessly captures and evaluates forecast accuracy metrics. It achieves this by comparing system-generated forecasts with user-applied adjustments across various channels. The resulting reports highlight areas that require demand management attention, offering valuable insights into forecast performance.
-
Dynamic Replenishment Strategies
The system diligently examines the present inventory and considers the expiration dates of each lot, automatically fine-tuning order quantities to align with the customer service level objective and supporting Just-in-Time replenishment principles. It offers visibility into potentially perishable inventory and excludes such items from network transfer suggestions. The system generates alerts to prompt user review and action for items requiring attention. Moreover, it produces a report highlighting inventory nearing expiration, providing an opportunity to offer discounts or promotions on items at discounted prices to reduce potential losses and move products quickly. This strategic approach frees up working capital and optimizes outcomes for sellers and customers.
Optimal product safety stock is achieved through a truthful consideration of various factors, including lead times by day of the week, variations in lead times by day of the week, the application's recommended ordering frequency cycle for a specified time horizon, the actual order cycle employed for placing orders, demand fluctuations over days in a week and week to week, the magnitude and frequency of demand, and several other pertinent factors.
Fresh food inventory benefits from dynamic replenishment—a process facilitated by the software's real-time data analytics. It helps grocers adjust orders quickly and efficiently, responding to the actual consumption patterns and minimizing the risk of overstocking perishable goods.
-
Reduced Waste and Enhanced Sustainability
The system optimizes the utilization of available network inventory by carefully analyzing and recommending transfers where there's a need, inventory availability, and economic and operational feasibility. This strategic approach minimizes capital tied to inventory, reduces waste, lowers costs, and enhances customer service levels. The application, guided by configured maximum inventory constraints, ensures that suggested orders never lead to overstock, promoting efficient and effective inventory management.
The application's intelligent management of source changes minimizes waste and enhances sustainability. Using a strategic approach, the system reduces inventory by considering the SKU exposure period and expected demand usage. As the source change date approaches, it maintains a zero on-hand balance at the current source while preparing inventory at the new source, minimizing waste. This seamless execution, without manual intervention, preserves SKU service levels and aligns with sustainability goals, proving invaluable in operational adjustments like rezoning the network of locations, supplier changes, and distribution center activities for a more efficient supply chain.
SKU with ramp-down scenario, depleting available inventory by the last week of May
By optimizing fresh food stock levels, the software directly reduces food waste, a significant issue for retailers and the environment. Efficient inventory management means fresher produce on the shelves and less spoilage, contributing to sustainability goals.
-
Improved Customer Satisfaction
By establishing business rules per requirements, the system offers ample flexibility to automate forecasting and ordering processes for designated product categories. The application selectively alerts users only when deviations from configured business rules are detected, providing detailed impact metrics. In cases where a product unexpectedly goes out of stock, such as supplier unavailability, the software intelligently identifies and automatically adjusts order quantities to accommodate additional inventory needs upon the product's return to stock, all without directly impacting the forecast.
The software ensures that popular fresh items are always available, meeting customer expectations consistently. This reliability of in-stock availability, coupled with high-quality offerings, enhances overall customer satisfaction and loyalty.
-
Operational Efficiency
The software minimizes the need for user intervention by offering transparent insights into weekly and daily demand history, product expiration details, expected demand over a specified time horizon, and vendor order requirements within the system, consequently enhancing the efficiency of the inventory management team. It adeptly manages and showcases key customers and their demand patterns compared to the total product sales.
The system can dynamically calculate and employ the optimal unit of measure when initiating orders, aiming to reduce overall costs throughout the supply chain. This involves comprehensively comparing handling costs, carrying costs, demand patterns, and other relevant factors. Consequently, it enhances warehouse management operations, including improving receiving and putaway processes. Furthermore, the system enhances labor planning efficiencies and supplier performance by generating insightful and user-friendly reports, facilitating seamless communication with suppliers and distribution center operation teams.
SKU, where the application chooses optimal UOM automatically as the Layer for improving operational efficiencies
Streamlined forecasting and replenishment processes mean staff can spend less time guessing stock levels and more time on customer service and other value-adding activities. It also reduces the financial burden of unsold inventory, boosting overall operational efficiency.
Conclusion
The task of managing fresh food inventory in grocery retail is complex and demanding. Manhattan’s Demand Forecasting and Replenishment software brings a game-changing solution to the table, blending advanced technology with user-friendly functionality. By maximizing freshness, minimizing waste, and ensuring customer satisfaction, the software not only addresses the specific challenges of fresh foods but also drives larger business objectives like sustainability, customer loyalty, and profitability. In an industry where freshness is a key differentiator, leveraging the right technology can be the deciding factor in a grocer’s success.
Related Insights
Grocery
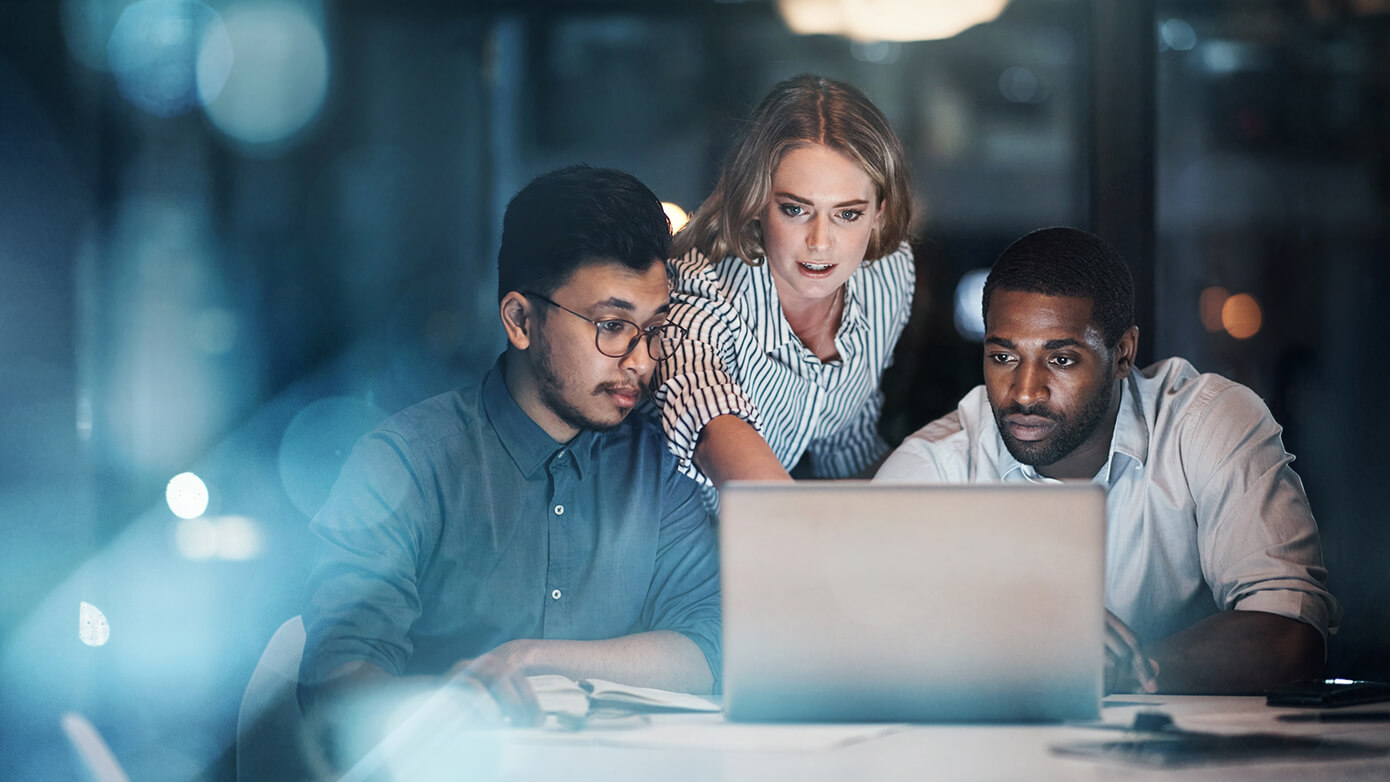
Demand Forecasting
A hybrid approach to forecasting that seamlessly blends the power of proven statistical models with cutting-edge AI.
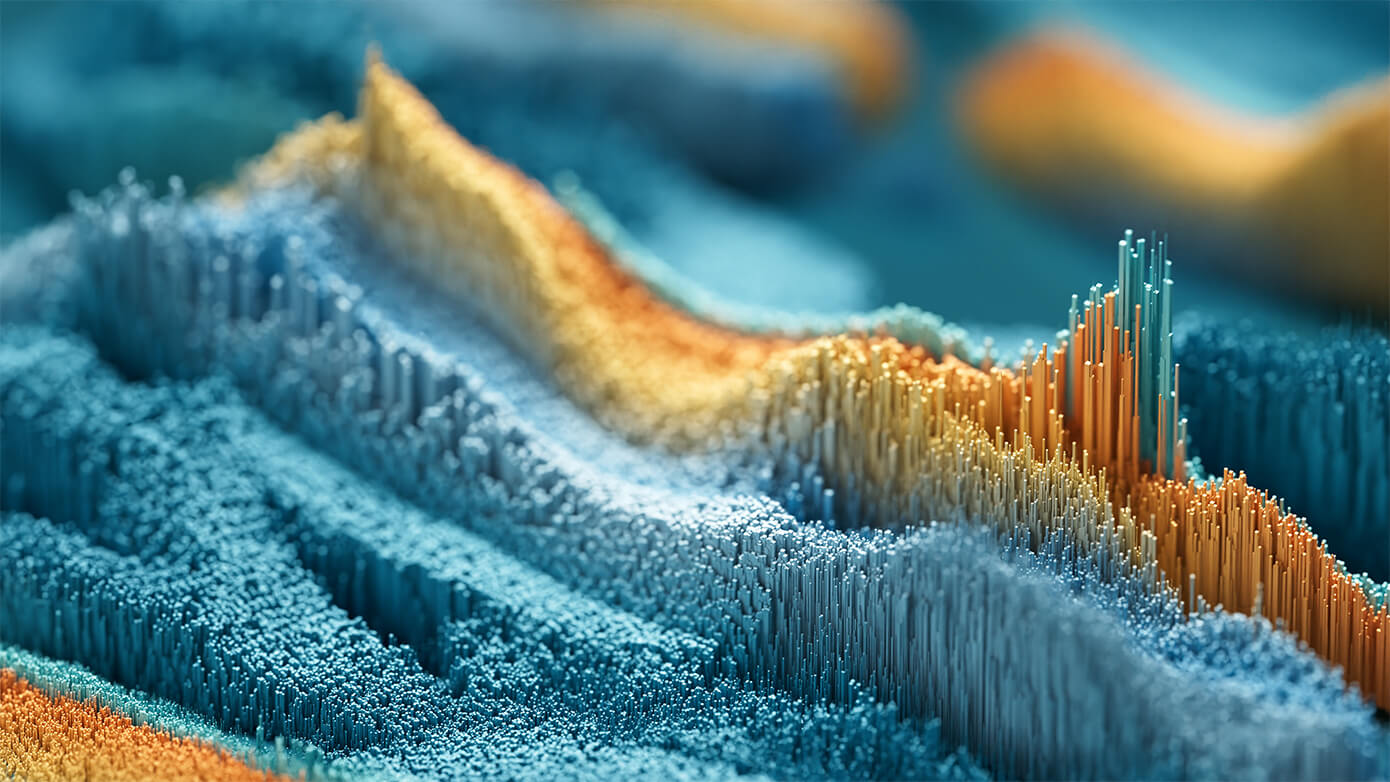
Replenishment
Seamlessly integrates AI-driven insights with real-time data to autonomously optimize inventory levels across all channels, ensuring the right products are always in the right place at the right time, without the need for manual intervention.